|
|
|
GH2000 driver with A4 motor changed to A4I motor need to cha
GH2000 series with A4 motor to A4I motor description
First, the reason for the change: For the company from 2015 to stop using the A4 Domokawa encoder motor, to avoid battery problems, the full use of A4I Danaher mechanical encoder configuration servo motor.
Second, the connection diagram:
2.1, GH2000T-LB2 series with A4 motor connection diagram:
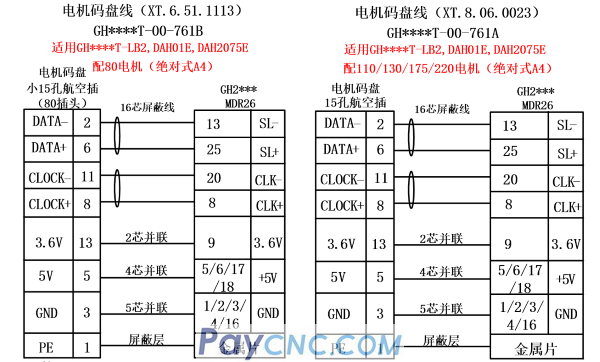
2.2, GH2000 series with A4I motor connection diagram:
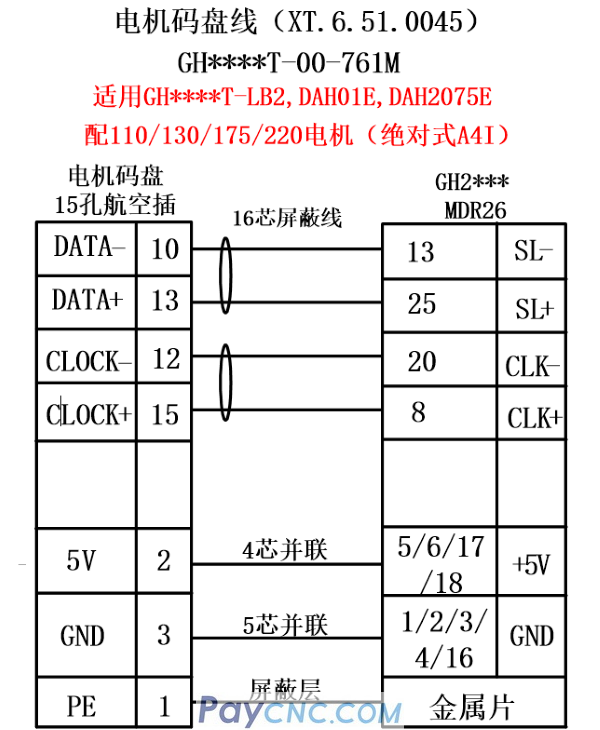
Third, servo parameter adjustment procedure description:
-
4.3.3 Motor Type Write-in
When the new motor or the Err-18 alarm occurs, the drive unit only can be identified (refer to the Chapter Four for motor corresponding code) after the corresponding types are written to the EEPROM, refer to the following items:
-
-
After the encoder line changes, the system communication needs to be disconnected (unplug any connected GLink communication line).
-
Write the motor model code from the GH2000 into the motor encoder as follows:
-
After the parameters are written, if the V514.5 version is below the motor zeroing,the V520 version above does not need to be zeroed. The mechanical connection needs to be released before zeroing. The steps are as follows:
-
Change the password and change PA-0 to 510:
-
Modify the operating method to change PA4-4 to 4;
-
Zero, tune to the Co- menu, press and hold the return car for about 3 seconds after the"FINISH"appears and the motor jitters, indicating that zeroing is successful, press the return key to use
-
Attention:
-
There is no need for internal enabling before zeroing
-
If the motor is empty (not connected to any mechanical construction), this will damage the drive unit
-
PA-99 is the zero voltage setting, the higher the voltage of the value of the monthly large zero voltage, the default value of the ordinary motor can be, for the inertia of the motor, can be appropriately increased zero voltage
-
After zeroing is successful, Dp-Apomonitors the menu, at which point the encoder's ±within 100
-
Reconnect to GLink,after the system is powered on, change parameter 4010 to 4096, write down parameters 4212,4213,4215 in an emergency stop by changing the system parameter 4001 to 0lvP to 1 and then change to 1 to restore the defaultparameter. Restore the noted parameters after the recovery is over. That is, the replacement is complete.
|
|
|
|